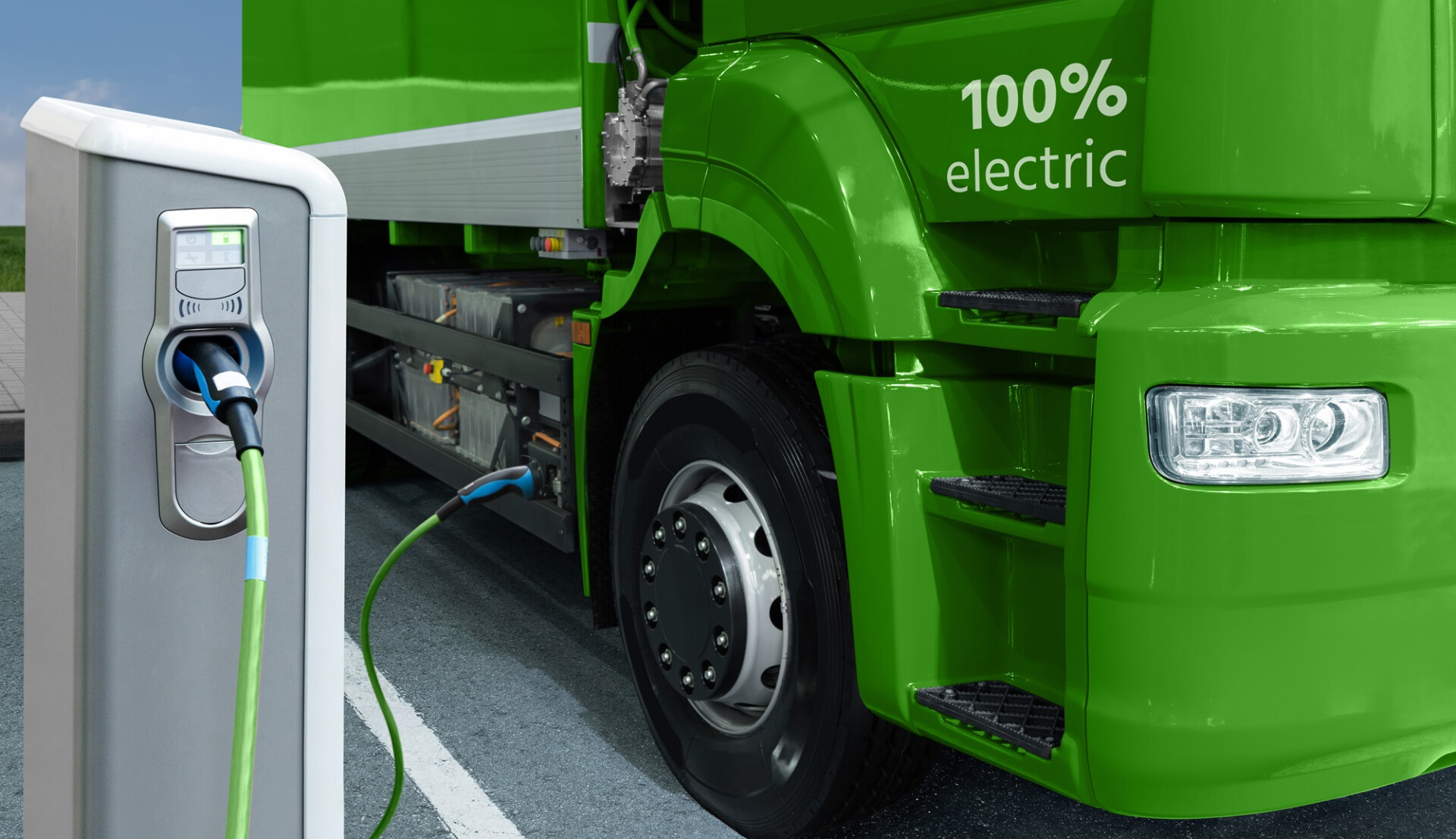
Industrial Transportation
Discover the future of industrial transportation & mobility
Dukosi Cell Monitoring System (DKCMS™) can deliver the performance and reliability gains needed for the next generation of batteries that will power industrial transportation and mobility applications such as agricultural, mining, marine, military vehicles, off-road utility vehicles, forklifts, and industrial robotics.
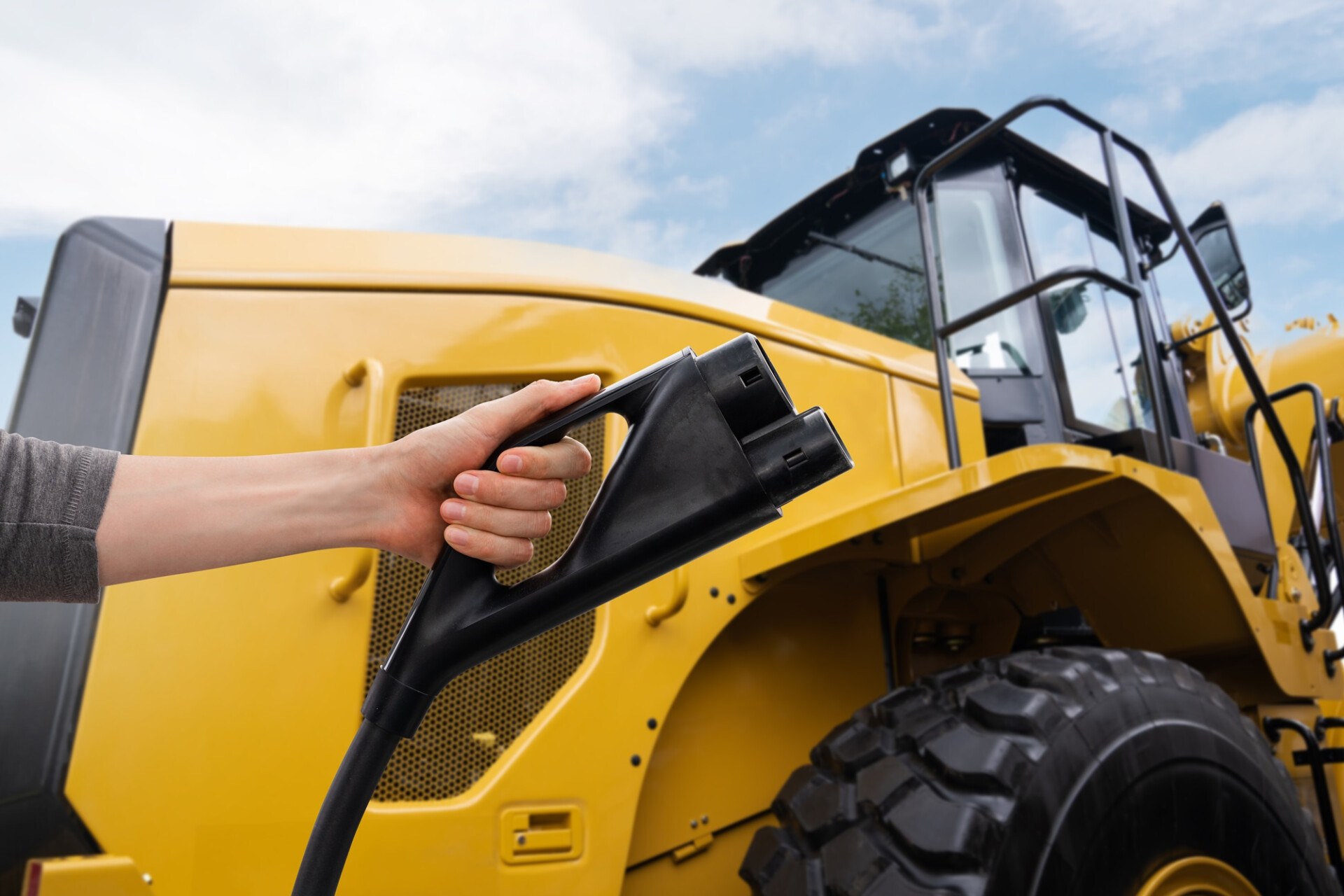
Extract more usable energy per pack
With each Dukosi Cell Monitor providing synchronized, highly accurate, detailed granular information of each cell’s behavior and lifetime status, DKCMS provides better insight into a battery pack’s long-term use. This gives industrial vehicle and robotics manufacturers more confidence to unlock greater utilization from each cell while ensuring longevity, slowing or reducing the drop in range over the life of the vehicle.
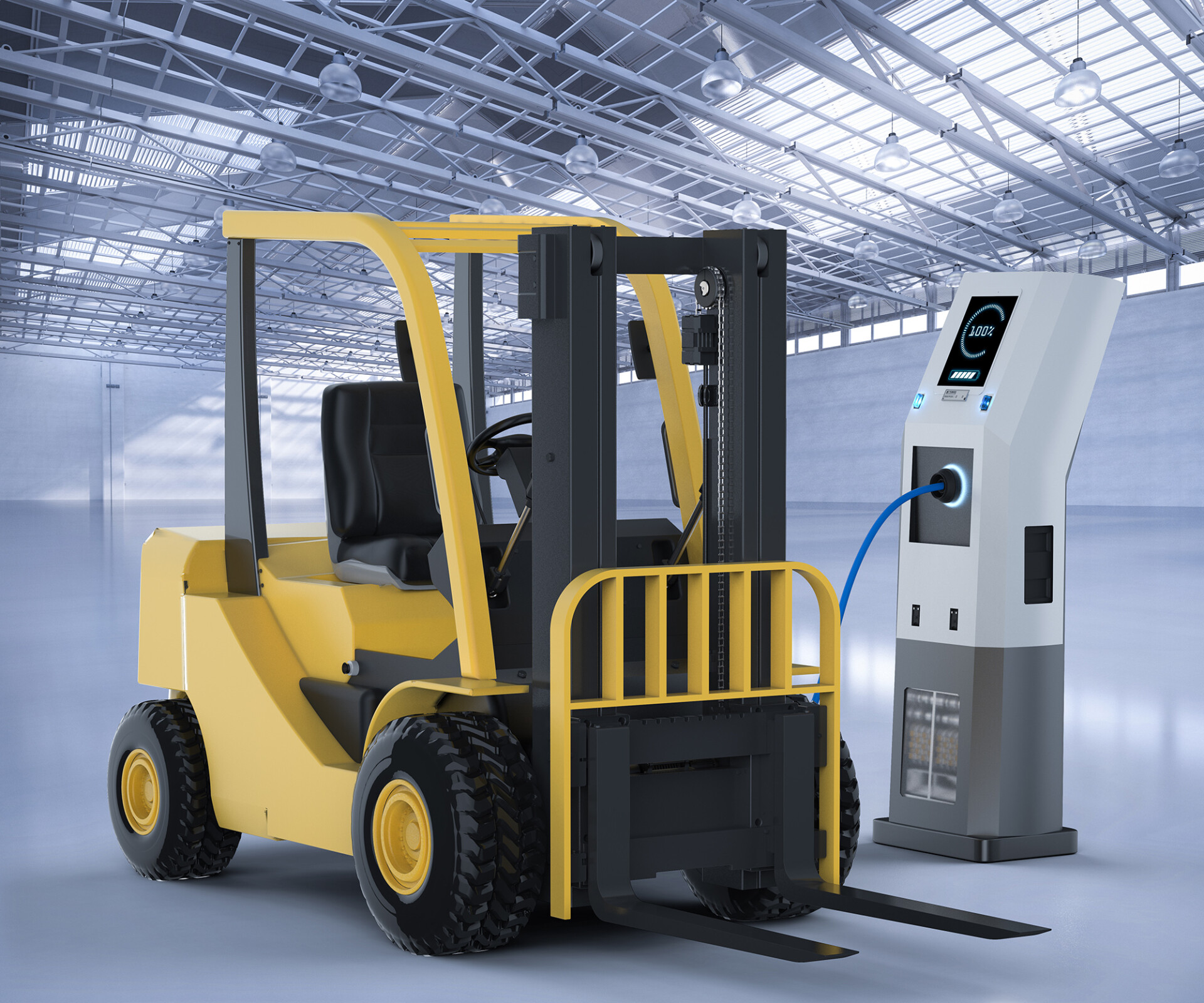
Reduce weight, improve reliability
By eliminating the complex wiring harness, supplementary PCBs, connectors, module assemblies, and other associated components, DKCMS enables battery pack weight reduction and reliability improvements. This results in a simpler, streamlined battery design. The reduction in weight and improved data quality can enhance the range, while still meeting the same reliability and warranty standards.
Flexible and scalable architecture
Vehicle designers and OEMs can scale easily to address different markets with changes to battery capacities and chemistries without requiring full revalidation thanks to DKCMS. Forgoing the limitation of a modular architecture, they benefit from the flexibility of singular cell increments connected using reliable C-SynQ® communication from the Dukosi System Hub residing on the central BMS host.
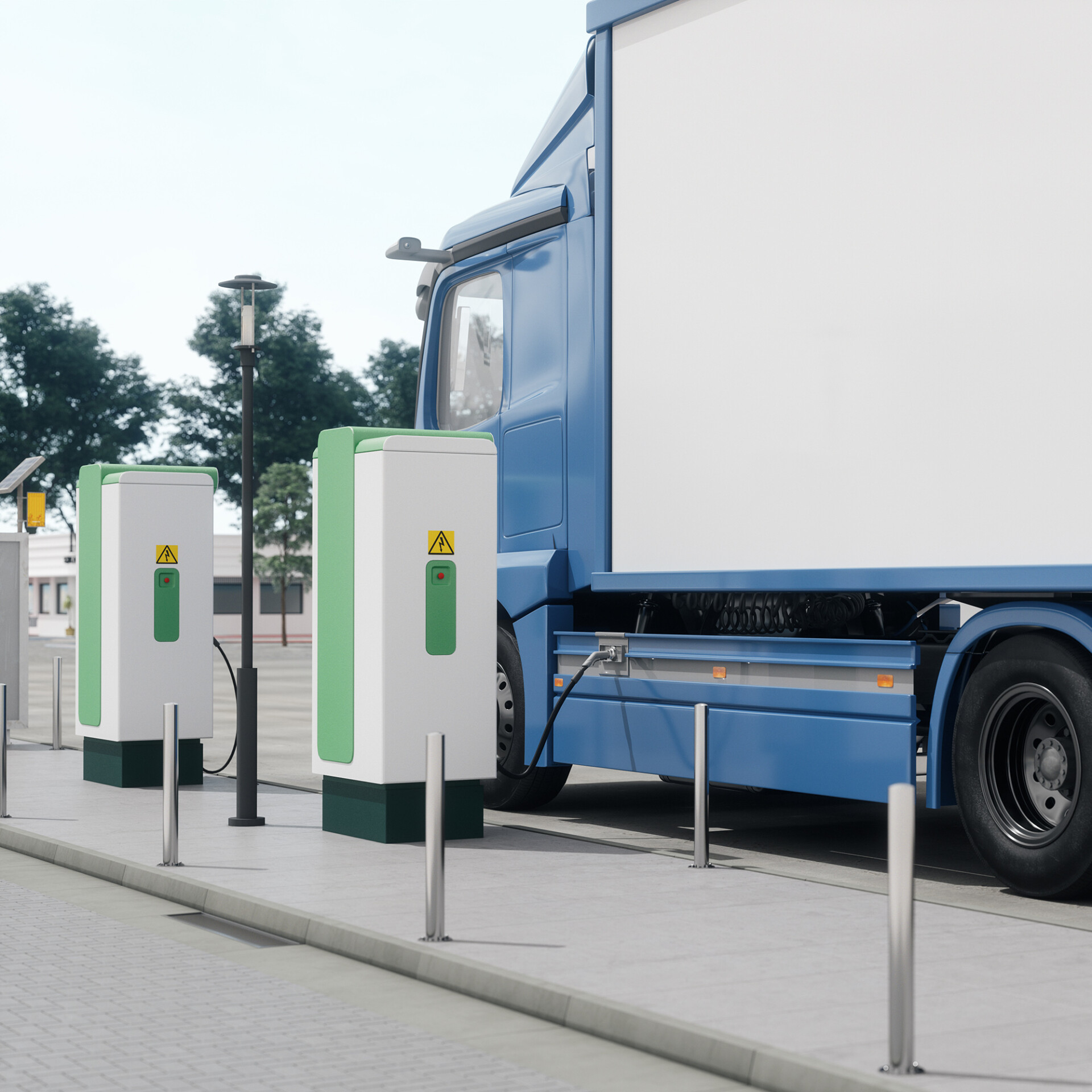
Accelerate time-to-market
Enabling cutting-edge battery integration designs like cell-to-pack and cell-to-chassis, DKCMS provides essential flexibility to accommodate sudden market changes. This allows for easy adaptation to vehicle configuration changes, resulting in a more dynamic and reactive solution that can make the competitive difference.
Enhance battery safety
Allowing every cell in the battery pack to be monitored 24/7, even when the main BMS host is in a low-power state, DKCMS provides immediate detection and alert to cell-level problems and enables earlier fault diagnosis, creating a safer, more reliable electric vehicle. This detection is at least 5 minutes earlier than battery packs without cell-level temperature measurement, which can be crucial to give more time for people to act in response to events such as temperatures outside safe zones. If necessary, the Dukosi solution can wake the host controller at any time, even if the vehicle is unattended during shipping or parked in a garage, for example.
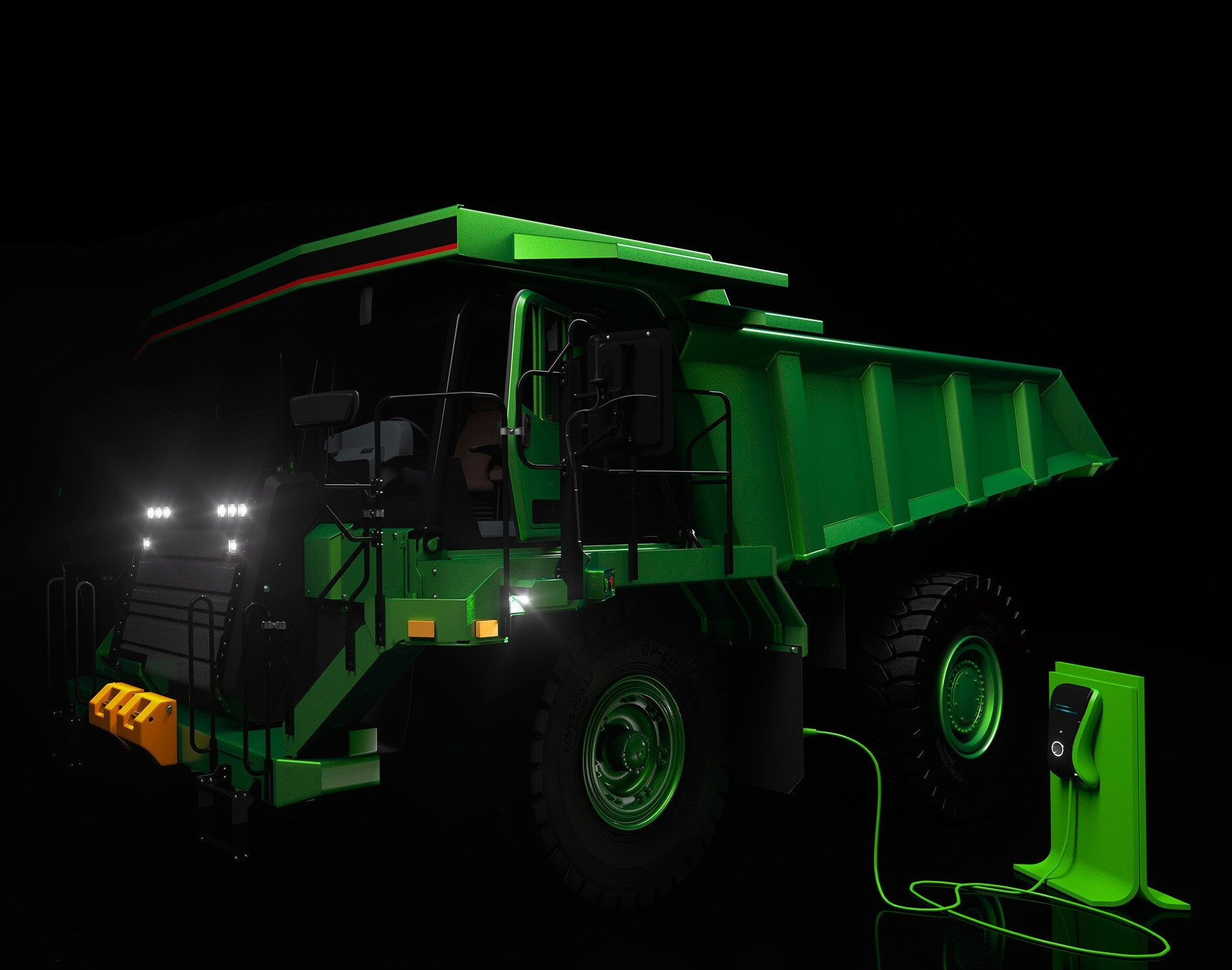
Reduce costs, optimize and automate manufacturing
DKCMS requires fewer components per battery pack, which in turn simplifies the manufacturing process and supply chain, reducing materials costs, and it can potentially enable a fully automated assembly line by eliminating time-consuming manual assembly line steps when installing wires, connectors, and pins.
Promoting a circular economy and sustainable battery chain
By capturing and storing lifetime data on each cell, the DKCMS promotes a circular economy (reduce, reuse, recycle) throughout the battery value chain. When the Dukosi Cell Monitor is implemented at an early stage in cell manufacturing, the solution offers lifetime traceability and helps OEMs to show compliance with the latest regulations. In addition, the lifetime usage data, including any extreme excursion events, are stored, yielding further advantages such as better cell grading, residual value assessment, and safer and more cost-effective second life usage or recycling.
Working with Dukosi
At Dukosi, we are driven by our mission to bring revolutionary changes to battery-powered applications. To achieve this, we put active collaboration into practice at technical, operational and strategic levels with our customers and partners. Our partners have been selected based on shared commitment to innovation and excellence, and their ability to deliver strong and trustworthy solutions that help accelerate customers’ development efforts and expedite time to market.