Promoting the Safe, Reliable, and Sustainable Electrification of Industrial Transportation
Industrial and commercial vehicles move trillions of dollars in materials and goods and are essential to global economies. However, these vehicles are also currently a major contributor to greenhouse gases (GHG). For example, in the United States, road transportation for commerce and industry is overwhelmingly the largest contributor of GHG emissions1, so we must urgently work to reduce these emissions, but without impacting essential economic activity.
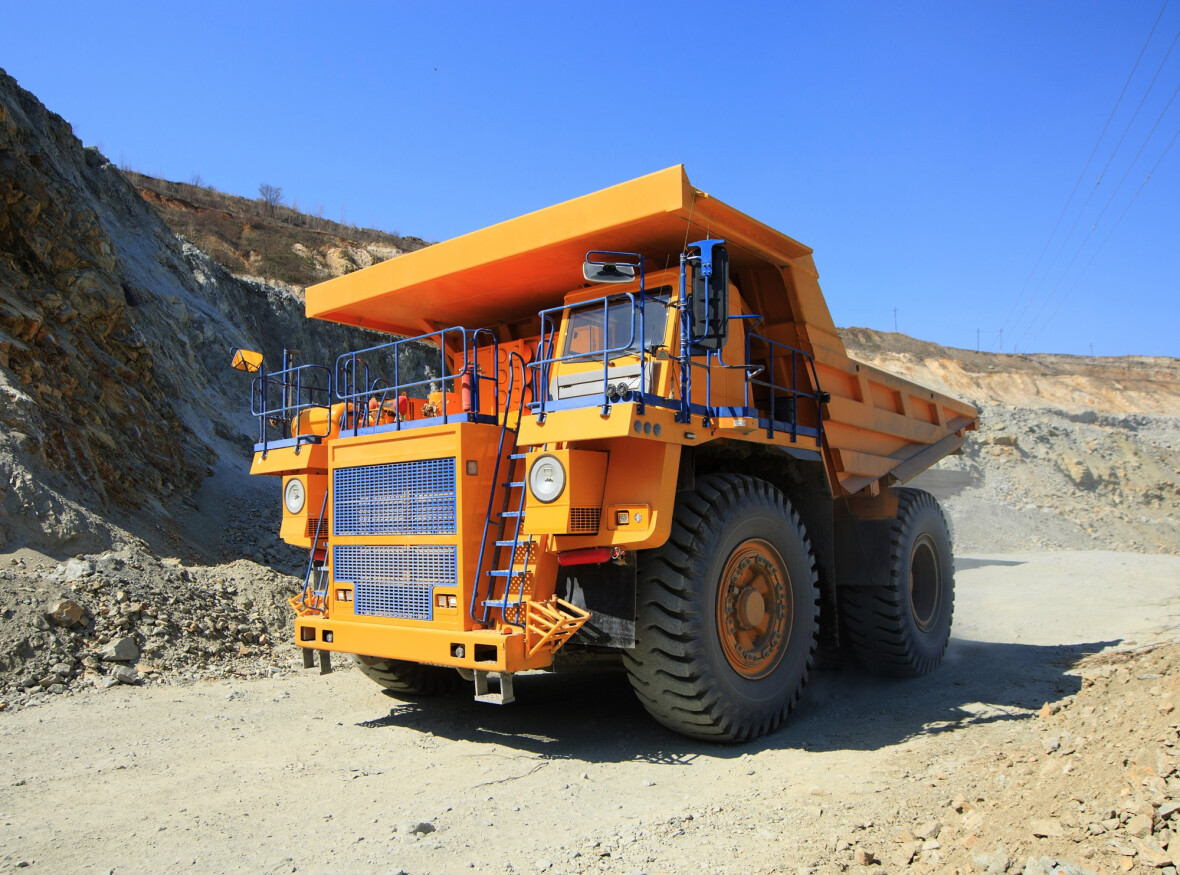
Decarbonization through electrification
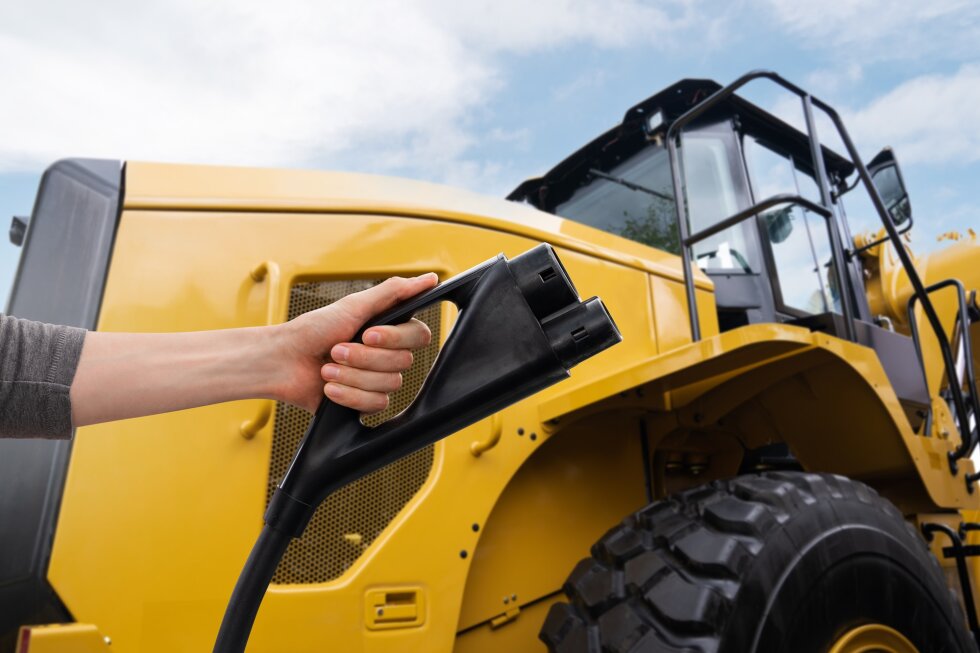
Embracing electrification, particularly when supported by green energy generation, can significantly drive decarbonization efforts: a fully electrified mine – including an electrified fleet of vehicles – powered by renewable sources could reduce its carbon footprint by 60-80 percent2. As a secondary safety benefit, swapping diesel engines for electrification eliminates local air pollution and significantly reduces noise pollution, improving working conditions particularly in enclosed areas.
Thankfully, electrification in the mining industry, as well as in construction and agriculture, is already progressing, with a healthy 27.1%3 cumulative annual growth rate (CAGR) forecast.
The challenges of electrifying industrial vehicles are different to road vehicles; the drivetrain requirements, and by extension the battery requirements, vary greatly depending on the specific application. For example, whereas a large mining haulage vehicle is typically used as frequently as possible to maximize productivity, an agricultural vehicle might only be used seasonally, but are reported to use up to 50% more energy3 in their tasks than equivalently sized machines in construction and mining. However, the need for greater flexibility in battery designs is at least supported by the typically large size and weight of industrial machines, where the batteries themselves can even become part of the required ballast in some instances.
Economic advantages compelling change
McKinsey4 estimates that, based on the total cost of ownership (TCO), battery electric vehicles (BEVs) will outperform their internal combustion engine (ICE) counterparts across all vehicle classes as early as 2025. One of the world’s largest mining companies, BHP, has recently committed to an electrified transition of its fleet of giant haulage trucks, starting in 2028. With analysts estimating that electrification of the mining industry could reduce energy (fuel) costs by up to 70 percent, and reduce maintenance costs by approximately 30 percent2, it’s easy to understand why.
As BEVs experience rapid development through sustained investment, these advantages should only grow over time. Many potential technological advancements are occurring throughout the electric drivetrain, particularly in the battery, which constitutes a significant part of the vehicle’s cost, performance, safety, and reliability. Moreover, any battery architecture must accommodate the diverseness of industrial vehicles through inherent flexibility and scalability, avoiding bespoke solutions that exhibit greater cost and risk.
Having been designed from the ground-up for large capacity, high voltage batteries, with safety, reliability, lifetime performance, and cost-effectiveness advantages, the Dukosi Cell Monitoring System (DKCMS) is an ideal solution for industrial vehicles as it offers unparalleled flexibility and scalability to meet the needs of construction, mining, agriculture, off-road utility vehicles, and even marine applications.
Dukosi Cell Monitoring System (DKCMS)
Flexible Integration Advantages
Whereas on-road vehicles typically have a common shape and size due to strict regulations, which limits variations in pack design, industrial and off-road vehicles are tailored more precisely to their application, so exist in forms of much greater variety. Therefore, using a battery architecture that’s inherently flexible and scalable – like DKCMS – is an essential asset, because redesigning a battery for multiple applications with changes to a physical layout, the number of cells, or the cell chemistry all requires considerable cost and time.
In part, it achieves this by forgoing the modules for cells used in batteries, which limits flexibility. DKCMS supports single cell increments and connects them with a contactless interface routed throughout the whole battery, promoting not just capacity flexibility, but a greater degree of freedom in physical layout, too. With its unique near-field connectivity and Dukosi C-SynQ® communication between Cell Monitors and BMS host via the System Hub, the battery architecture is simplified, to the benefit of integration.
Its architecture allows design adjustments without having to revalidate the entire battery – a key advantage in time to market and cost management. The Dukosi Cell Monitors are ideally installed on each cell and can support any cell chemistry, including common NMC, increasingly popular LFP, and even emerging technologies such as Sodium-ion.
Enhanced Safety & Reliability
Industrial equipment is designed for long hours of hard work, often in difficult or harsh conditions, so reliability is paramount to ensure worksites keep operating. DKCMS promotes reliability by up to 2X compared to a typical wired battery BMS design by reducing the component count by up to 10X. This is achieved through the elimination of complex wiring harnesses, supplementary PCBs, connectors, and module assemblies, among other items, and replacing them with a contactless architecture that uses reliable near-field connectivity with Dukosi C-SynQ communication. This allows a battery to withstand constant vibrations and the regular knocks, bumps, and hits these vehicles take without crucial components inside becoming disconnected.
Other architectural advantages include synchronous cell data transmitted with predicable latency, which provides the BMS host more accurate and reliable data to act on. Meanwhile, per-cell temperature monitoring can identify any cell performing outside safe parameters much earlier, potentially alerting for preventative maintenance.
Safety goes hand-in-hand with reliability, and if a cell experiences elevated temperatures outside the safe operating range it can be identified much earlier than battery packs without cell-level temperature measurement, which can be crucial to give more time for the BMS host to issue alerts to operators.
Cost Advantages
DKCMS enables numerous cost advantages throughout the lifetime of the cell and its application.
During cell manufacturing, it streamlines processes and makes the time-consuming cell formation more efficient. In battery pack development, it can reduce material costs, and design and validation time, accelerating time to market. During operation, Dukosi’s highly accurate and synchronous cell measurements allow the BMS host to act on more reliable data to extract more usable energy from each cell, allowing for smaller and lighter batteries with the same energy per pack, while also enhancing reliability with earlier warnings of any cell-level problems.
Furthering sustainability through a circular economy
Beyond first-use advantages, these batteries also often contain difficult-to-obtain metals or require energy-intensive mining of raw materials, so enabling a circular economy must also be considered in electrification efforts. In this regard, Dukosi Cell Monitors can store the provenance information of every cell in the battery, promoting sustainability through next life uses before eventual recycling, maximizing the potential life of each cell.
In order to hit sustainability targets, whether due to local regulation or corporate environmental, social and governance commitments, vehicle parts should be reused where possible when they reach end of life. The battery is a prime target for reuse opportunities, as the cells inside could still hold plenty of capacity, ready for use in other applications. For example, by repurposing them for use in battery energy storage projects in other parts of the business can further reduce total cost of ownership (TCO).
To achieve this, DKCMS goes beyond battery-level state of health (SoH) insights to streamline the assessment of individual cell quality, through on-cell storage of histograms showing highly accurate, detailed information of each cell’s lifetime of use, including whether it has suffered events outside its specification. This enables accurate grading of each cell, promoting greater trust, safety, and reliability in second-life applications. For cells that must be recycled, provenance and materials information is similarly stored in the Cell Monitor, allowing recycling operations to optimize their processes to potentially recover more material.
Contact Dukosi to learn how our innovative battery architecture can enhance your next-gen industrial transportation application.
References
- Fast Facts on Transportation Greenhouse Gas Emissions – EPA.gov
- Electrifying mines could double their electricity demand – McKinsey
- Battery Markets in Construction, Agriculture & Mining Machines 2024-2034 – IDTechEx
- Why the economics of electrification make this decarbonization transition different – McKinsey