Maximizing Safety and Reliability in Batteries for eVTOL Aircraft
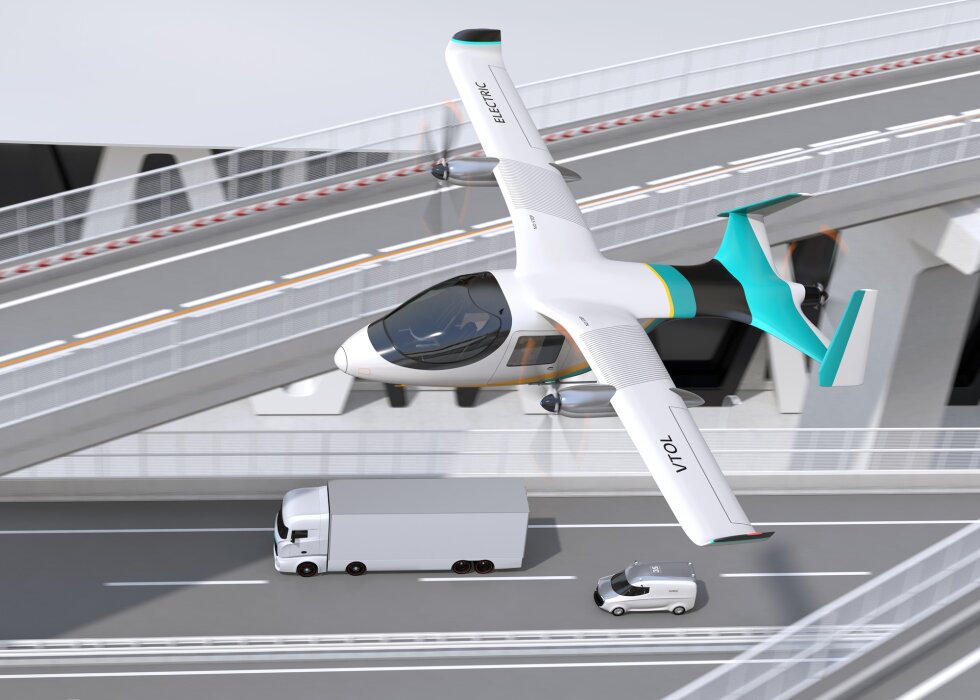
Electric vertical take-off and landing – eVTOL – aircraft represent an emerging class of battery-powered vehicles that offer distinct advantages to a segment of the air transport industry.
With zero CO2 emissions and low noise, they are ideal for short hops or routes that traverse urban or suburban areas where traditional aircraft would be considered a nuisance, or simply unviable.
In addition to fully electrified aircraft, there are other pathways for electrification in the aviation industry. For example, hybrid propulsion systems use batteries for VTOL phases and traditional fuel for cruising, or electric propulsion to maneuver conventional aircraft during taxiing—a process that is notoriously fuel-inefficient and significantly contributes to local air pollution near airports.
When developing new or significantly modified aircraft, operational safety and system redundancy is a primary consideration. In an industry that relies heavily on tried-and-tested technologies, incorporating novel designs presents considerable challenges. Therefore, adopting solutions explicitly designed to maximize safety and reliability in battery systems can accelerate development.
Addressing the Challenges of Electric Aircraft Batteries
Due to the limited energy density of current batteries compared to traditional aviation fuel, numerous small-format lithium-ion cells and/or large-capacity lithium-ion cells are required in order to provide sufficient power for even short-range flights. Designing batteries for electric aircraft presents unique challenges, as batteries must endure aggressive duty cycles with discharge demands of up to 6C, putting great pressure on their design. Additionally, these batteries must operate under challenging environmental conditions, such as temperature extremes, vibration, and mechanical shock experienced during landings.
The Importance of Monitoring Every Cell’s Temperature
During fast charging and discharging, hot spots can develop in weaker cells, further accelerating damage. Monitoring the temperature and voltage of every series cell increment is essential for maximizing safety and reliability. Traditional battery architectures do not inherently offer this functionality, typically limiting temperature sensing to a few thermistors per battery pack.
The Dukosi Cell Monitoring System (DKCMS), however, attaches a Cell Monitor to every series cell increment, and in fact supports up to three temperature sensors per series cell increment. This provides comprehensive end-to-end coverage, even for larger “blade-style” cells and high numbers of paralleled cylindrical cells. To learn more, read the results from our lab simulations[i], and real-world experiments in our case study[ii] on the effects of temperature propagation in cell modules, and why per-cell temperature monitoring is an essential safety asset.
Accelerating R&D with Three Temperature Points per Series Cell Increment
DKCMS can accelerate the early stages of battery development by providing three temperature datapoints per Cell Monitor. With one temperature sensor built into every Cell Monitor and support for two additional external thermistors, DKCMS enables measurement comparisons between cells in the core and on the perimeter of a paralleled group. This can be used to help to evaluate the effectiveness of thermal management designs, as for instance, in a 200s battery, DKCMS can deliver real-time readings from up to 600 temperature sensors.
Accurate State of Charge (SoC) and State of Health (SoH)
In battery-powered applications, the range and health of a battery are determined by the State of Charge (SoC) and State of Health (SoH), respectively. Since these metrics rely on real-time calculations, consistent, accurate and synchronous cell data throughout the battery’s life is critical. Dukosi excels in this area, providing industry-leading voltage sensing accuracy (TME), and direct temperature measurements. For further insights, read our whitepaper on the sensitivity of lithium-ion battery SoC and SoH estimates to sensor measurement error and latency.[iii]
Reliability Improvements
DKCMS has been designed from the ground-up for high-power, high-performance batteries. It uses a unique contactless architecture based on near field connectivity, with robust communications provided by our proprietary protocol called C-SynQ®[iv]. By eliminating wiring harnesses, pins, and connectors—which are common failure points—DKCMS delivers up to twice the reliability of typical wired battery architectures.
The near field connectivity uses a single bus antenna placed within a few centimeters of each Cell Monitor, which provides wired-like connectivity without the drawbacks of physical connections, ensuring synchronized cell readings and deterministic data delivery to the Battery Management System (BMS).
Accommodating Space Constraints and Weight Distribution with Flexibility and Scalability
Traditional battery designs use cells grouped in modules, and modules laid out into a single, rectangular battery mass. While sufficient for road vehicles, e-aircraft often require distributed mass within the airframe, making it difficult to accommodate fixed battery shapes. Dukosi’s contactless solution offers unparalleled flexibility for layouts, even in three dimensions, as the bus antenna can be routed in any direction. Moreover, eliminating the need for cell modules allows batteries to scale in single-cell increments, providing precise adaptability for capacity, weight, or layout needs, as well as compatibility with advanced architectures like cell-to-pack (CTP), cell-to-chassis (CTC), or indeed, cell-to-airframe.
The Dukosi Cell Monitoring System (DKCMS) is ideal for eVTOL and electric aircraft batteries as it delivers superior safety, reliability, flexibility and scalability beyond traditional battery architectures. Learn more about the advantages of DKCMS[v], and how it compares to other battery architectures in our white paper.[vi]
[i] https://www.dukosi.com/blog/monitoring-the-temperature-of-every-cell-to-maximize-safety-and-performance-of-high-power-batteries
[ii] https://www.dukosi.com/blog/case-study-importance-of-per-cell-temperature-monitoring-to-maximize-safety
[iii] https://www.dukosi.com/blog/sensitivity-of-lithium-ion-battery-soc-and-soh-estimates-to-sensor-measurement-error-and-latency
[iv] https://www.dukosi.com/blog/what-is-dukosis-c-synq
[v] https://www.dukosi.com/dukosi-cell-monitoring-system-dkcms
[vi] https://www.dukosi.com/blog/white-paper-wired-wireless-and-contactless-comparing-bms-design-approaches