Enabling Safer and Sustainable Electrification of Airport Ground Support Equipment (GSE)
The aviation industry is experiencing considerable growth as air travel continues to increase and airports expand operations to keep pace with the rise in global tourism, business travel, and trade. At the same time, sustainability is high on the agenda as the global airport industry faces increasing pressure to reduce its carbon footprint. This provides opportunities for innovation and technology solutions to support green initiatives and make airports more sustainable.
Ground Support Equipment (GSE) are the backbone of airport operations, playing a pivotal role in making the movement of passengers, baggage, goods, services, and aircraft as safe and as efficient as possible. As airports expand their operations to accommodate increasing traffic and handle aircraft movement, there are opportunities to implement green initiatives when adding new terminals, gates and passenger service equipment or upgrading existing ones.
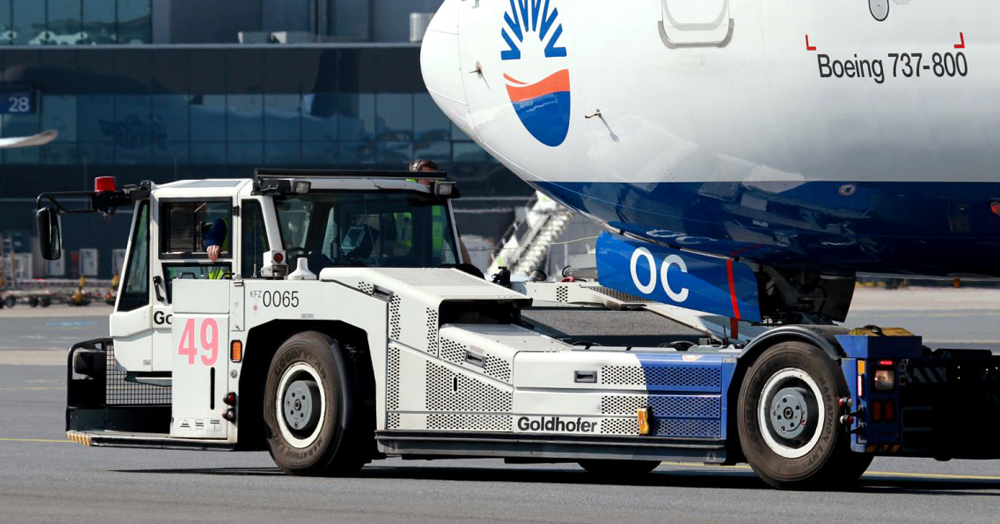
Electrification of Ground Support Equipment
GSE are rapidly becoming electrified (eGSE), in part supported by government funding for purchasing zero-emission vehicles and installing the necessary charging infrastructure. For example, in 2024, the EU allocated €1.3 billion to projects at 21 airports1, aligning with the ambitions of the EU Green Deal.
Frequent start-stopping, short trips, and idling are textbook benefits of electrification over traditional fuels, while the high torque of electric motors is ideal for ferrying heavy loads, and the distances are limited to the few square miles of airport area. Electric vehicles require less maintenance, and with market data indicating that EV batteries last longer than previously expected, the total cost of ownership decreases the longer equipment can be used. Even beyond the immediate operational advantages, eGSE also contributes to a reduction in local noise and air pollution, directly benefiting the health and safety of staff and passengers.
The demanding working environment of an airport means that reliability and safety are two key considerations for eGSE, and battery architecture is a key contributor to this. Moreover, due to the limited market size, battery architecture must accommodate the diversity of eGSE vehicles through flexibility and scalability, avoiding bespoke solutions that exhibit greater cost and risk.
The Dukosi Cell Monitoring System (DKCMS™)2 is designed from the ground up to maximize performance, reliability, and safety in high-performance batteries, while also being inherently flexible and scalable for various battery sizes and layouts. This allows it to adapt to actual needs, easily accommodating different application scenarios, system functions, and performance requirements.
The simplicity of the DKCMS architecture also means that repairs are streamlined. Instead of working around a complex wiring harness, the single bus antenna makes maintenance faster. The embedded database within the chip-on-cell allows for easier maintenance and streamlines repurposing of cell modules for different load applications.
Enhanced Reliability..
eGSE equipment must be robust, reliable, and available to work in all environmental conditions. DKCMS improves battery reliability by up to 2X compared to a typical wired battery BMS design by reducing the component count by up to 10X. This is achieved through the elimination of complex wiring harnesses, supplementary PCBs, connectors, and module assemblies, among other functional items, and replacing them with simplified, yet robust, near field connectivity. This allows a battery to effectively withstand vibrations, knocks, and bumps that these vehicles can experience during daily operations without crucial internal components becoming weakened or disconnected. Another DKCMS architectural advantage is Dukosi C-SynQ®3 proprietary communications, which can capture all cell data synchronously and transmit it with deterministic latency to the BMS host, providing the BMS host with more accurate and reliable data to calculate SoX, enhancing performance and long-term battery health.
..and Safety!
DKCMS can accommodate even very large batteries with up to 216 cells, yet still goes above and beyond traditional battery architectures by integrating at least one temperature sensor for every cell in the battery.
Battery designers have the flexibility to add an additional two thermistors per cell, providing extended coverage for larger surface area cells, such as blade-style pouch or prismatic formats. If any cell experiences temperatures outside the safe operating range or compared to its neighboring cells, it can be identified much earlier than legacy battery architectures with only one or two temperature sensors per module, which can be crucial and give more time for the BMS host to issue alerts to operators. This not only improves safety during operation but also during charging; vehicles can be supported by fleet management operations that manage charging and watch for any condition that requires preventative maintenance.
More accurate and fine-grained temperature sensing can also benefit low-temperature environments, as pre-conditioning of the battery to an appropriate temperature before charging ensures cell health, reliability, and lifespan are maximized. It’s important to ensure that all cells reach the correct temperature range and remain within that temperature during the charging session.
Learn more4 about how battery safety is enhanced when measuring the temperature of every cell.
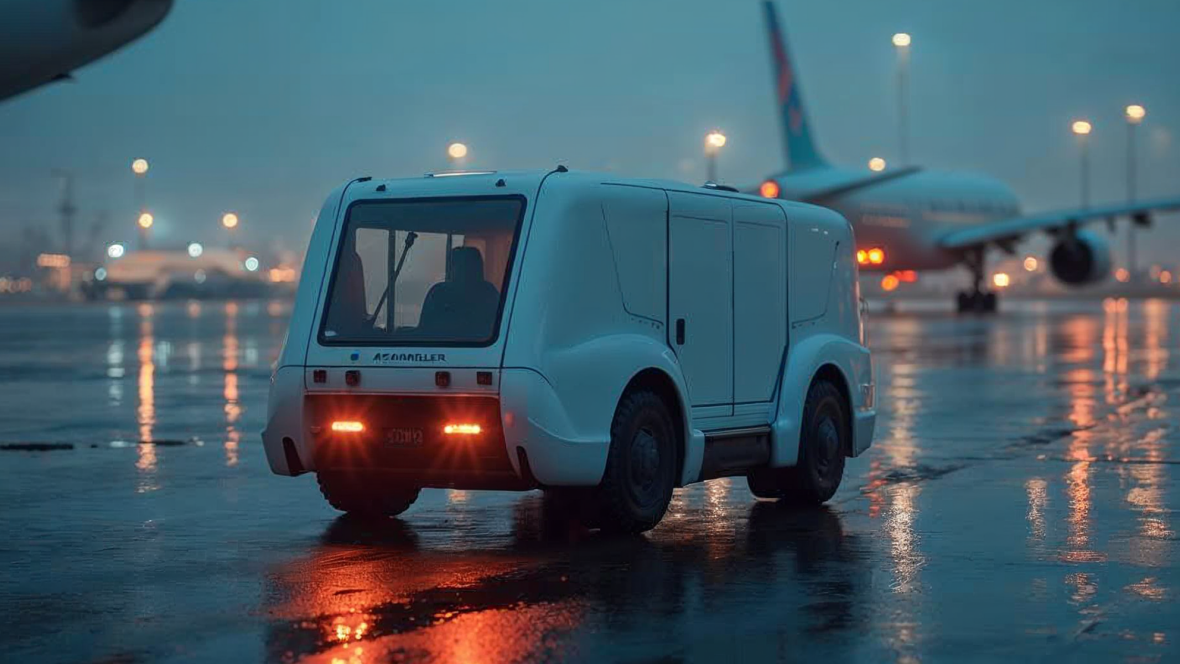
A Flexible and Scalable Architecture
GSE are often single-application equipment; while some are adapted from standard road-going vehicles, others, such as tractors for maneuvering aircraft, are highly specialized. Adapting the custom design to electric requires more ingenuity. This is where a flexible battery architecture benefits, because while traditional batteries are a large flat package, DKCMS can – if needed – be oriented more freely to fit a given space, or even to perform double duty as ballast if required. The advantage of DKCMS single nearfield bus antenna means that it can be routed throughout the pack to meet each individual Cell Monitor, even if the cells form an unusual arrangement. DKCMS even allows a battery to scale by one cell at a time, giving much greater control over the design, unlike modular designs which are limited to 12-24 cell adjustments. Other advantages come from the Dukosi Cell Monitors supporting virtually any cell chemistry, including common NMC, increasingly popular LFP, and even emerging technologies such as Sodium-ion, providing flexibility to quickly adapt to changes in supply or local market conditions.
Unlocking Additional Value
In addition to DKCMS reducing material costs with a simplified battery design, unlike other battery architectures that use far field wireless communications, it allows design adjustments without having to revalidate the entire battery – a key advantage in time to market and cost management.
During vehicle operation, the highly accurate and synchronous cell measurements give the BMS host greater confidence to extract more usable energy from each cell, allowing for smaller and lighter batteries with the same energy per pack compared to other architectures, or by using it as spare capacity to enhance longevity from the same addressable kWh.
Extending the eGSE advantage with Dukosi technology
Whatever the vehicle type and wherever the environment, DKCMS with C-SynQ enhances eGSE to be as safe, reliable, and effective as possible, benefiting not just operators, but staff and passengers as well.
..in a battery pack that’s already available today!
CAMY has collaborated with Dukosi to develop a high performance battery expressly designed for airport ground support vehicles5, promoting their electrification, and thus the sustainability of airport environments. Using the Dukosi Cell Monitoring System (DKCMSTM) with C-SynQ® technology, CAMY has developed a new battery pack design called “KUINETIC”6 that’s highly scalable and flexible, while also enhancing the safety, reliability and long-term performance compared to alternative battery architectures. This battery pack is being deployed in new service equipment and will roll out across airport ramp operations worldwide.
Contact Dukosi to learn how the innovative DKCMS battery architecture can enhance next-generation eGSE designs.
- https://transport.ec.europa.eu/news-events/news/eu-boosts-zero-emission-mobility-over-eu424-million-funding-42-projects-2024-04-10_en ↩︎
- https://www.dukosi.com/dukosi-cell-monitoring-system-dkcms ↩︎
- https://www.dukosi.com/blog/what-is-dukosi-csynq ↩︎
- https://www.dukosi.com/blog/monitoring-the-temperature-of-every-cell-to-maximize-safety-and-performance-of-high-power-batteries ↩︎
- https://www.dukosi.com/press-release/camy-launches-next-generation-battery-pack-for-gse-applications-at-inter-airport-southeast-asia ↩︎
- https://www.dukosi.com/blog/case-study-reliable-safe-scalable-and-sustainable-battery-packs-for-gse-in-airports ↩︎