Case Study: Reliable, Safe, Scalable, and Sustainable Battery Packs for GSE in Airports
Ground Support Equipment (GSE) are the backbone of airport operations, playing a pivotal role in making the movement of passenger services, baggage handling and aircraft as safe and as efficient as possible. As the aviation industry faces increasing pressure to curb its environmental impact, airports are looking to GSE solutions with electrification, automation, and predictive maintenance technologies to ensure seamless operations and enhanced safety across terminal and ramp operations. This shift not only improves the working environment for employees and the experience for passengers by enhancing local air quality and reducing noise, it also aligns with sustainability goals.
Electric ground support equipment (eGSE) batteries must be robust, reliable, and available to work in all environmental conditions, while maintaining the highest safety and security standards, ease of maintenance, and serviceability. As GSE vehicles are built to fit their unique applications, the batteries for eGSE applications should ideally fit the vehicle, rather than requiring the vehicle to be expensively redesigned around a typical EV battery architecture and shape.
CAMY has collaborated with Dukosi to develop a high performance battery expressly designed for airport ground support vehicles, promoting their electrification, and thus the sustainability of airport environments.
CAMY “KUINETIC” battery pack for eGSE vehicles achieves class-leading compact size, robustness, reliability and safety.
Using the Dukosi Cell Monitoring System (DKCMS™) with C-SynQ® technology, CAMY has developed a new battery pack design called “KUINETIC” that’s highly scalable and flexible, while also enhancing the safety, reliability and long-term performance compared to alternative battery architectures.
By bringing intelligence to every cell with voltage and temperature tracking, DKCMS captures greater battery data insights, streamlining predictive maintenance and serviceability, providing long-term benefits such as greater uptime, and lower total cost of ownership (TCO).
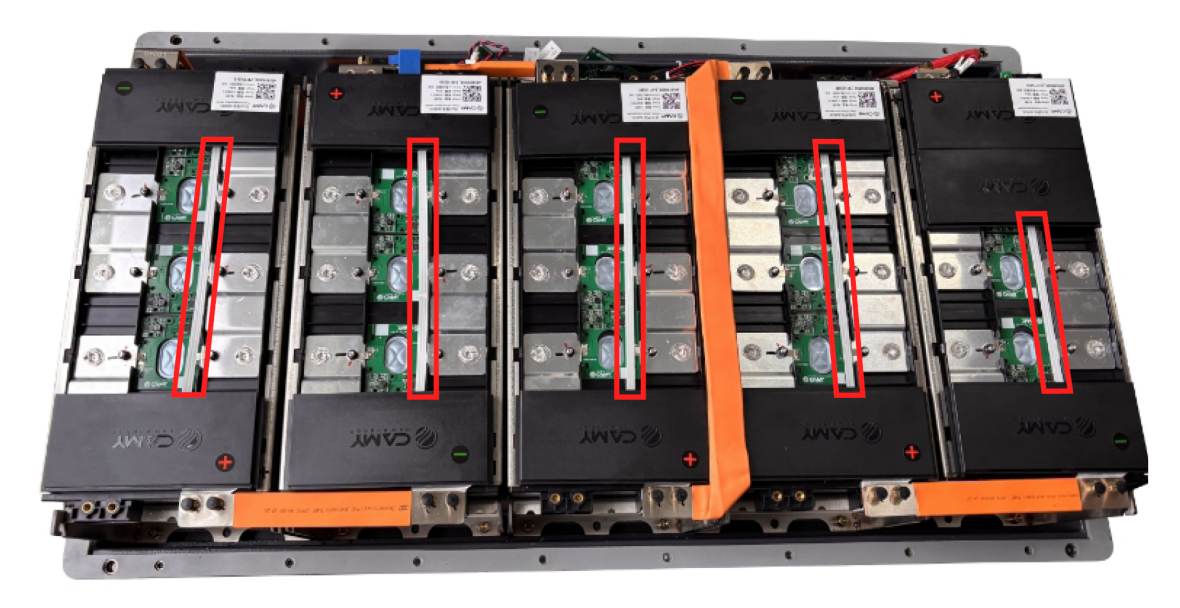
DKCMS single bus antenna (highlighted red) is routed back and forth over the Dukosi Cell Monitors, enabling reliable contactless C-SynQ® communications from every cell
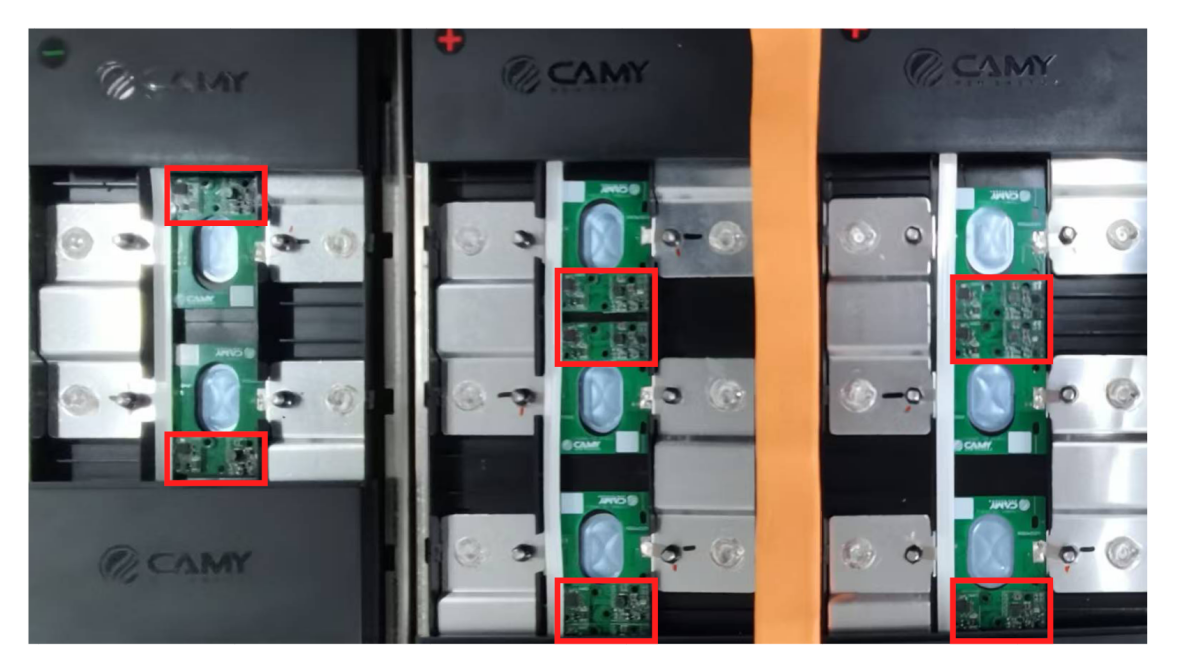
Each cell is affixed with a Dukosi Cell Monitor (highlighted red) that accurately measures cell voltage and skin temperature. All cell data is captured synchronously and transmitted with deterministic latency via C-SynQ communication via Dukosi System Hub to the BMS host processor.
Achieve More with DKCMS
Scalability and Flexibility
Unlike other battery architectures DKCMS is scalable at the cell-level and can be applied to a shape, size and weight (via diverse cell chemistry/format support) that precisely fits the vehicle, allowing for much greater freedom of design customization.
Safety
DKCMS can accommodate even very large batteries with up to 216 cells. Unlike other battery architectures that use only one or two temperature sensors per several cells, DKCMS integrates at least one temperature sensor for every cell in the battery, providing unparalleled insights into battery operation, immediately identifying any cell experiencing temperatures outside its safe operating range. This provides more time for the BMS host to issue alerts to fleet operators, thereby improving safety and reliability by potentially triggering preventative maintenance.
Reliability
When designing the battery, DKCMS reduces the component count by up to 10 times compared to a typical wired BMS, increasing reliability by up to 2 times. During operation, Dukosi C-SynQ® captures all cell data synchronously and transmits it with deterministic latency to the BMS host. This provides more accurate and reliable data to calculate state of charge (SoC) and state of health (SoH), enhancing performance and long-term battery life.